If you’ve ever managed a manufacturing team, then you know the challenge of creating and keeping up with shift schedules.
After all, there are so many nuances to consider: fulfilling employee preferences, meeting peak production goals, and making sure the staff is never overworked or underutilized. As much as we might like it to be easy-breezy, in reality, work scheduling can feel overwhelming.
But have no fear!
With this comprehensive guide on manufacturing shift scheduling, you’ll soon be able to conquer even the toughest shifts with ease – so grab your sharpest pencils, and let’s get started. ✍️
What Is a Manufacturing Shift Schedule?
A manufacturing shift schedule is the plan for a manufacturing plant’s staff operations, usually enacted on a daily or weekly basis. It designates who is working when and in which departments, as well as who is taking breaks and going on vacation.
Changeovers can be complicated in manufacturing plants when considering the number of workers and machines involved. Thankfully, a proper shift schedule helps to keep everyone organized and make sure that no time or resources are wasted during the production process. It’s like having an invisible supervisor hovering over everyone to confirm that everything is running smoothly – that’s efficient!
Types of Manufacturing Shift Schedules
Different types of shifts may be more suitable depending on the particular industry:
- For short-cycle operations which must produce products with high speed and accuracy, it may be best to use a single-shift operation or two-shift rotation.
- If a factory works for extended periods and requires large amounts of output, then three-shift rotation can maximize operations efficiency.
There are additional benefits to different shift patterns, but in the end, it all comes down to which situation makes sense in the long run. And no matter the type of operation, adjusting scheduling practices can ultimately help enhance productivity and safety on the manufacturing floor. So, choose your shift type wisely! And check out these examples for inspiration:
Rotating shifts 🔁
Rotating shifts can start at any time of day and last anywhere from a few hours to twelve. Essentially, it means that employees come in as the clock rotates – like a never stopping wheel of fate. While this shift scheduling model doesn’t offer employees a consistent schedule and requires them to show a considerable level of adaptability, it certainly keeps the factory running – and that’s what matters!
2-3-2 shifts 🌞🌚
A 2-3-2 shift in manufacturing involves a rotating schedule that consists of employees working two days, followed by three days off, and then two days or even nights on.
The purpose of this type of shift is to ensure that the factory is staffed 24 hours a day, seven days a week. What’s more, the system equally divides the load across two teams (day and night) so workers don’t overexert themselves – everyone deserves their weekends.
This type of system isn’t just cleverly efficient, it helps make factories with tight budgets run smoother and keep the production process steady, which is always an added bonus.
DuPont Shifts ♾️
The DuPont shift schedule is designed for businesses with the objective of streamlining operations and optimizing productivity in a given period of time. It involves four teams and follows this pattern:
- Four 12-hour night shifts,
- Three days off,
- Three more days of work,
- One day off,
- Three nights of work,
- Well-deserved one-week vacation.
The logic behind this type of shiftwork is pretty straightforward: the rotating shift pattern results in 24/7 coverage and increases production efficiency while ensuring adequate rest periods for employees. Overall, if your organization is looking for a way to boost productivity and keep costs under control, it may be time to explore whether a tripartite shiftwork system like the DuPont work schedule could be right for you.
Graveyard shifts 👻
Graveyard shifts can certainly sound like something out of a horror movie. Yet, despite the name, graveyard shifts don’t actually take place in graveyards (unless you happen to work in a cemetery). Instead, they simply occur overnight and into the early morning hours.
Graveyard shifts are popular for a lot of businesses, as there are fewer distractions and less competition at such hours. Despite this, graveyard shifts can be rough and often require workers to push the boundaries of their willpower in order to make it through… So, in the end, aren’t they the stuff evil villains’ dreams are made of?
Split shifts ➗
Split-shift production in manufacturing is an ingenious way to get more out of the same resources. It’s like having a two-for-one deal but with your workforce instead of groceries.
Splitting shifts into two different times of the day or night allows employees to work during their peak productivity times. Plus, split shifts are a great option for businesses where machines frequently need extra maintenance or rest periods during which employees have no work to do.
All in all, it’s a flexible system that helps maximize employee output while minimizing costs because the same staff works when it is most effective and needed.
Manufacturing Shift Scheduling: Best Practices
Estimate 🔮
No matter what approach to manufacturing shift scheduling you take, there’s always a risk of overestimating your production capability and overworking your staff. Therefore, it’s vital to make sure you’re operating with accurate forecasts and estimates, which in turn should be informed by data-driven insights.
Knowing the realities of both demand and capacity can help your teams gain an edge when it comes to planning out the days ahead. With the right estimates at your disposal, you can create an efficient production system that doesn’t sacrifice quality or leave your staff feeling exploited.
Plan ahead 📅
One of the best ways to ensure a smooth transition between employee shifts is to plan ahead. When your personnel is aware of its daily tasks and upcoming deadlines, group confusion is eliminated, and maximum efficiency is promoted.
Having a plan already in place when it’s time for shift changes will not only give everyone a headstart but also allow you to go beyond your regular productivity quota, giving yourself some added cushion in case anything goes awry. So don’t be like the hare and get caught napping – use your wise foresight and plan ahead!
Follow the law ⚖️
Being aware of the legal framework within which you operate is of utmost importance when planning out a shift schedule. After all, no factory foreman wants to find themselves facing an unexpected lawsuit because they misread an obscure labor statute.
As Benjamin Franklin once said, “An ounce of prevention is worth a pound of cure” – better to read up and be aware ahead of time than to land yourself in hot water. So, prepare for shifts by spending some time with your local regulations and outlining expectations clearly enough that everyone on the team can avoid any encumbrance from well-meaning but uninformed industry watchdogs.
Communicate 💬
We all know that communication is key – that’s true even when it comes to minimizing endless headaches associated with manufacturing shift scheduling. That’s why so many savvy managers prioritize open and frequent channels of dialogue, whether they’re shouting across the factory floor or talking through sophisticated online tools.
Communicating early and often isn’t just a polite practice. It helps ensure that everyone’s needs are addressed proactively and leads the team to better scheduling decisions when problems arise. In other words, communication gets the gears of production running smoothly.
Track leave time 🌴
One of the most important steps in making sure shift changes go off without a hitch is to always track each employee’s leave time.
An effective system for tracking leave time will help you plan ahead with certainty – better decisions about employees’ shifts can be made since you know exactly when someone is and isn’t available. This eliminates one of the big unknowns that can be so stressful during shift scheduling or last-minute changes.
Having this information correct and up-to-date can make all the difference when it comes to ensuring your manufacturing runs as smoothly as clockwork.
Use technology 🤖
The best way to address your manufacturing shift scheduling issues? Get tech savvy and use technology!
In addition to helping save time in the long run, versatile apps, databases, and data tracking systems can revolutionize a factory’s management process. Whether it’s payroll, employee tracking, or shift organization – utilizing technologies provides the opportunity to automate processes and ensure things are done right. After all, why manually do what technology can do much better?
Streamline Manufacturing Shift Scheduling with actiPLANS
Need to get the production line rocking again? actiPLANS is here to save the day!
This employee scheduling software streamlines manufacturing shift scheduling, allowing you to quickly and easily allocate your team resources and incorporate schedule changes in an instant. Instead of relying on traditional methods that are inefficient, you can apply actiPLANS and save yourself a lot of time and energy by easily creating a visual timeline of employees’ shifts – each optimized for individual availability.
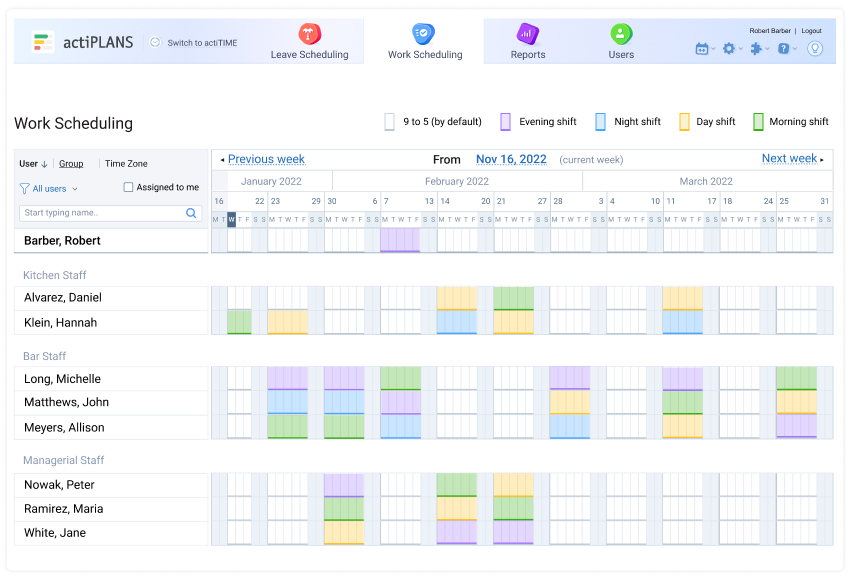
In addition to that, actiPLANS lets you speed up team communication thanks to up-to-date automatic email notifications on changes made to employee schedules. Besides, it allows you to keep track of your team’s leave time and run informative reports, which makes it simpler than ever to be mindful of your resource allocation decisions.
With actiPLANS, tedious scheduling turns into a piece of cake! So, sign up for a free online trial, and give it a go.