Do you ever feel like your business doesn’t have enough hours in the day? Or that working harder and faster isn’t getting you anywhere close to where you need to be? Well, it could be because of a lack of capacity planning.
Capacity planning is an integral part of any successful business endeavor and understanding how to use it correctly can help make sure that all the pieces are lined up for future success. It involves setting goals, budgeting for resources, forecasting growth trends and efficiently utilizing personnel within their scope of work.
In this comprehensive guide, we’ll cover everything you need to know about this essential process, including handy capacity planning tools and practical advice on making the most out of your current manpower!
- What Is Capacity Planning?
- Capacity Planning vs. Resource Planning
- Key Types of Capacity Planning
- Questions That Capacity Planning Helps to Answer
- Why Do You Need Capacity Planning?
- Main Approaches to Capacity Planning
- Primary Capacity Planning Strategies
- Useful Capacity Planning Techniques
- The 5-Step Capacity Planning Process
- How to Calculate Production Capacity: Example
- Handy Capacity Planning Tools
- Best Practices for Capacity Management
- Conclusion
What Is Meant by Capacity Planning?
Simply put, capacity planning is the process of determining the appropriate amount of resources needed to meet the demands of an organization.
It ensures that a business can maximize its performance while meeting all customers’ wants and maintaining operational efficiency without running into the dreaded “out of stock” nightmare or overexerting itself.
However, capacity planning is not just about making sure you have enough of everything. It involves finding the sweet spot where you’re not overstocking or tying up valuable capital, and not underestimating demand and missing out on potential sales.
It’s a delicate balancing act that requires a bit of mathematical prowess, a deep understanding of customer behavior, and a willingness to adapt and pivot as conditions change.
Capacity Planning vs. Resource Planning
Capacity planning
In addition to the above, capacity planning involves assessing the maximum level of output that a particular system, process, or operation can handle within a given time frame.
In other words, it’s all about figuring out just how much your business can handle before things start to buckle under pressure. This includes everything from physical infrastructure (like buildings and machinery) to human resources (like staff and their expertise).
Resource planning
Resource planning, on the other hand, is about defining what resources your business needs in order to meet its goals and how to manage the available resources in the best way possible. This involves identifying areas where your business is lacking something, and then figuring out how to acquire the resources necessary to fill those gaps.
So, how do these two concepts differ?
Well, while capacity planning is focused on figuring out the upper limit of what a given system can handle, resource planning is focused on figuring out what needs to be added in order to achieve a desired outcome.
Essentially, capacity planning is about making sure that your business isn’t pushed beyond its limits, while resource planning is about making sure that your business has everything it needs to succeed.
Questions That Capacity Planning Helps to Answer
- How many projects can we realistically take on in the next quarter without stretching our team too thin?
- What’s the maximum number of product units we can produce in a month with our current setup?
- Do we need to hire more staff to meet the expected demand for our new product line?
- How will a potential new project impact our current delivery timelines?
- Can our current IT infrastructure handle an increase in online sales during the holiday season?
- What are the risks if we exceed our production capacity?
- How can we adjust our processes to increase capacity without compromising quality?
- What’s the optimal way to allocate our resources across various projects to maximize output?
- How much buffer capacity do we need to maintain to accommodate unexpected orders?
- At what point should we consider expanding our facilities to keep up with growth?
Why Do You Need Capacity Planning?
1. Anticipate risks and opportunities
Capacity planning is not about predicting the future with 100% accuracy – that’s impossible. But it does give you a sneak peek into potential challenges and opportunities that lie ahead.
By analyzing trends, past performances, and current resources, you can identify risks like overloading your team or running into resource shortages before they become full-blown crises. On the flip side, it can also highlight opportunities for growth, like scaling up operations to meet predicted demand spikes without breaking a sweat.
2. Better understand your team
When you engage in capacity planning, you’re essentially mapping out everyone’s skills, availability, and current workload. This allows you to recognize individual strengths, preferences, or limits, and spot where you’re overloading someone or, conversely, where you’re underutilizing talents that could shine brighter on other tasks.
Ultimately, capacity planning lets you understand not just who is good at what but also who enjoys what they’re doing. This insight fosters better project assignments, more accurate time estimation, and a happier, more productive team environment.
3. Reduce costs
Capacity planning helps your business figure out exactly how much it needs in terms of resources, like tech and staffing, to get the job done efficiently without overspending. By predicting demand, you can adjust your resources to match and ensure you’re not paying for extras you don’t need.
It’s all about finding that perfect balance between too much and too little, which in the long run, saves a bunch of money.
4. Increase flexibility and scalability
Capacity planning lets you better understand what you have, what you’ll need, and when you’ll need it. This forward-thinking approach helps adjust to changes smoothly, whether that’s scaling up for a sudden surge in demand or scaling down during slower periods.
Basically, it’s like having an elastic band rather than a rigid stick – you can stretch or shrink your resources as needed without snapping. This kind of flexibility is invaluable as it ensures that you can pivot quickly without being hemmed in by your current resources.
5. Enhance the quality of production or service
Capacity planning helps you find out the best way to meet customer demand without overworking your team or machinery. By getting this balance just right, you can avoid the dreaded production hiccups, like delays or quality dips, maintaining the top-notch quality of your product or service every time.
In a nutshell, it’s all about being prepared and flexible, so when demand spikes or dips, you can address the change smoothly without putting too much effort or compromising quality.
What Are the 4 Types of Capacity Planning?
- Workforce planning – Personnel is the most vital resource for most organizations, and workforce planning specifically focuses on ensuring you have the right number of employees with the right skills to meet demand. This includes forecasting employee availability, hiring needs, training plans, and even budgeting for salaries and benefits.
- Facility planning – If your business relies on physical brick-and-mortar locations, you’ll need to make sure you have enough space to meet demand. Facility planning involves forecasting the growth of your business and making sure you have the necessary space and equipment to keep up.
- System planning – For businesses that rely heavily on technology (which, let’s be honest, is most of them these days), system planning is key. This involves forecasting your IT needs, including hardware, software, and network infrastructure, in order to keep things running smoothly.
- Product planning – This process is meant to determine how many people, machinery, and materials your business needs to meet the changing product demand. It involves calculating the maximum number of products you can actually make over a given period under normal working conditions. This way, you can align your work schedules, inventory levels, and other production capabilities with market demand and make sure that your business resources are utilized efficiently.
Main Approaches to Capacity Planning
- Strategic – This is the big-picture stuff. It involves assessing your company’s long-term goals, analyzing market trends, and making predictions about future demand. Strategic capacity planning helps companies prepare for growth and expansion.
- Tactical – This type of capacity planning is more short-term. It involves adjusting production levels to meet current demand. This is where efficiency and optimization come into play.
- Operational – This is where the rubber meets the road. Operational capacity planning involves managing day-to-day resources to ensure smooth production. This type of planning focuses on maximizing efficiency and minimizing downtime.
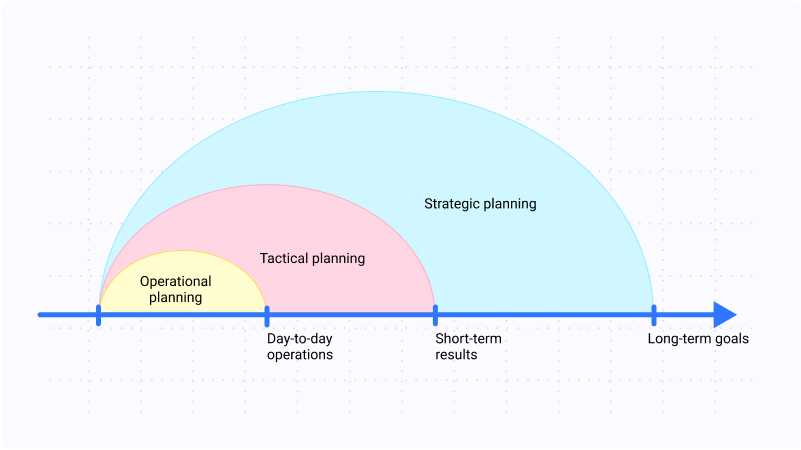
3 Primary Capacity Planning Strategies
1. Lead capacity planning
As its name suggests, lead strategy refers to leading the demand curve. It involves anticipating future demand and increasing capacity before it arrives, so you’re prepared to meet it head-on.
Example:
Let’s say you’re running a small bakery that specializes in creating delicious and intricate desserts. You’ve been in business for a few years and noticed that demand for your treats almost exceeded your ability to fulfill it during the last Christmas period. You’ve got a limited number of ovens and staff, after all, and only so many hours in the day.
This is where lead capacity planning comes in.
By analyzing your sales trends and projections, you can start to get a sense of how much demand you’ll be facing the next Christmas season. From there, you can make informed decisions about how to increase your capacity in order to meet that demand (i.e., you might decide to invest in additional ovens or hire extra staff members).
2. Lag capacity planning
Lag capacity planning is a strategy used by companies to minimize risks associated with variable demand and capacity constraints. It involves intentionally delaying the expansion of capacity until the need arises, thereby reducing wasted resources and excess costs.
Example:
Imagine a hotel that experiences peak demand during the summer season. Traditionally, the hotel might plan to expand its capacity by adding more rooms to ensure it can accommodate all the guests. However, with lag capacity planning, the hotel would wait until they observe a consistent increase in demand before adding more rooms. By doing so, the hotel will avoid overexpansion and the risks associated with it.
3. Match capacity planning
The match strategy allows businesses to maintain the balance between their capacity and customer needs without overcommitting resources during low-demand seasons or periods. It seeks to align capacity with demand in real time and match the anticipated demand with available resources as accurately as possible.
Example:
A canteen that services a university campus might use the match strategy by analyzing the number of students within a given period. It will also consider the average purchase by each student from day to day.
By understanding these key metrics, the canteen owner can optimize their production capacity to align with the expected demand. Hence, they will ensure they always have enough meals prepared to meet the demand without experiencing shortages or dealing with unnecessary waste.
4 Useful Capacity Planning Techniques
- Trend analysis – This technique involves tracking historical data to identify trends and patterns that can help predict future growth and demand. By analyzing historical sales figures, visitor logs, staff absences, or other relevant data, organizations can make reasonable projections about their capacity needs in the coming months or years.
- Resource utilization – This technique focuses on measuring and analyzing the utilization of existing resources to determine how efficiently they are allocated and implemented. This way, you can identify opportunities to optimize resource usage, maximize your output potential, and avoid unnecessary waste.
- Scenario planning – This technique involves creating multiple scenarios based on different possible outcomes and assessing the likelihood and potential impact of each scenario. It can help you identify potential risks and opportunities, and develop plans to mitigate or capitalize on them accordingly.
- Workload characterization – This methodology is about mapping out the workflows and processes involved in delivering products or services, and identifying potential bottlenecks or capacity constraints. By understanding how workloads are distributed across employees or other resources, you can optimize your capacity planning to ensure the right resources are available at the right time.
The 5-Step Capacity Planning Process
Step 1: Define expected demand
This is where you pull out your crystal ball and try to guess what your customers are going to want in the future. Look at past data, market trends, and any other factors that might affect demand. The key is to make an educated guess, not one based on wishful thinking.
Step 2: Estimate the required resource capacity
Once you have an idea of what demand will look like, you need to figure out how much you’ll need to produce to meet it and which resources will help you with that. Consider everything from physical resources like machinery and materials to human resources like staff and their skill sets. Crunch those numbers and make sure you have enough to meet demand.
Step 3: Measure your current capacity
Now it’s time to take a long, hard look at what you have. How much can you currently produce? Are there any bottlenecks or constraints that might limit production? Be honest with yourself – it’s better to know your limits now than to find out the hard way later.
Step 4: Identify the capacity gap
Once you know what you can do and what you need to do, compare the two. Is there a gap between what you can produce and what you need to produce? If so, how big is it? This will help you determine just how much work you need to do to bridge the gap.
Step 5: Match resource capacity with demand
Finally, figure out how to close that gap. This might mean investing in new machinery or hiring additional staff. Alternatively, you might need to adjust your production processes or streamline operations. Whatever it takes, make sure you align your resource capacity with demand to ensure you can keep up with all those hungry customers.
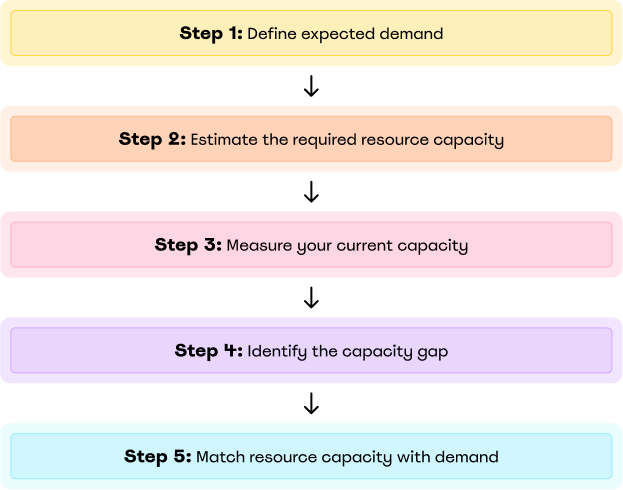
How to Calculate Production Capacity: Example
Alright, let’s break down capacity planning with a simple example.
Imagine you run a small bakery, and you want to ensure you’re baking enough buns and bread to meet demand, but not so much that you’re wasting resources:
- First up, you gauge how many customers you’re expecting. Suppose it’s around 100 folks a day, each buying 3 items on average. That’s 300 items per day.
- Then, calculate your current capacity. Perhaps, your oven can bake 50 items per hour, and you’re open for 8 hours a day. That gives you a total capacity of 400 items a day (50 items * 8 hours).
- So, what’s the gap? You need to bake 300 items, and your capacity is 400 items. Looks like you’re in good shape and can even handle a little spike in demand.
- If, hypothetically, demand doubles unexpectedly, you’d then need to bake 600 items a day. That would require you to expand your production capacity by either purchasing an additional oven or extending operating hours.
Remember, these are rough calculations. Real life can be more unpredictable, but this gives you a base to work from!
5 Handy Capacity Planning Tools
1. actiPLANS
- Leave management
- Work scheduling
- Time off reports
- Mobile app
- Automatic notifications
- Time tracking integration
actiPLANS is a top-of-the-line workforce management tool that can help with capacity planning and much more. It allows for effortless employee availability management while streamlining the resource scheduling process, reducing labor costs, and boosting overall productivity.
With actiPLANS, you can easily create resource schedules that are tailored to the needs of your business just perfectly. It features a visual timeline that displays employees’ time off, which makes it easy to plan out work considering employee availability and ensure that you have the right number of staff on hand to meet the varying demands of your business, without over- or understaffing.
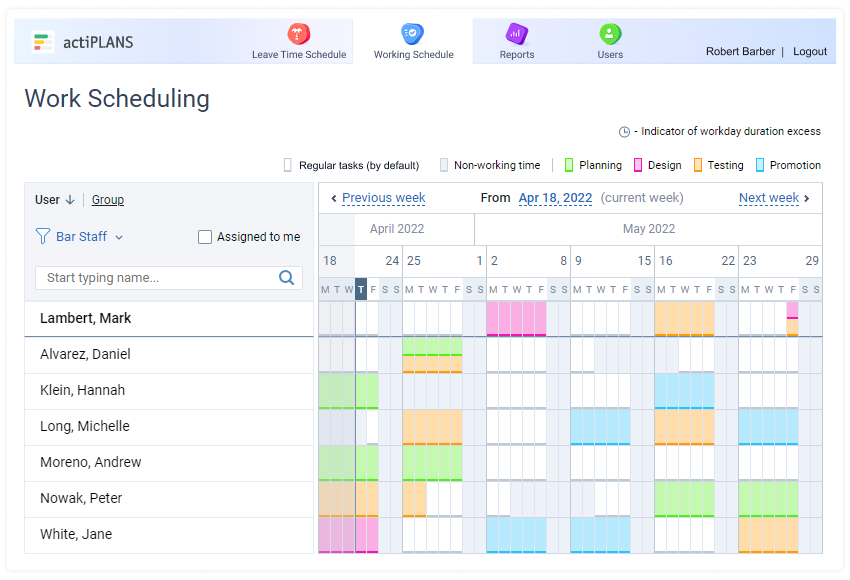
actiPLANS offers advanced reporting features that help to track employee attendance, analyze staff absences, and see trends over time. This data gives invaluable insight for making more informed decisions about your team’s capacity and identifying areas where you can improve productivity.
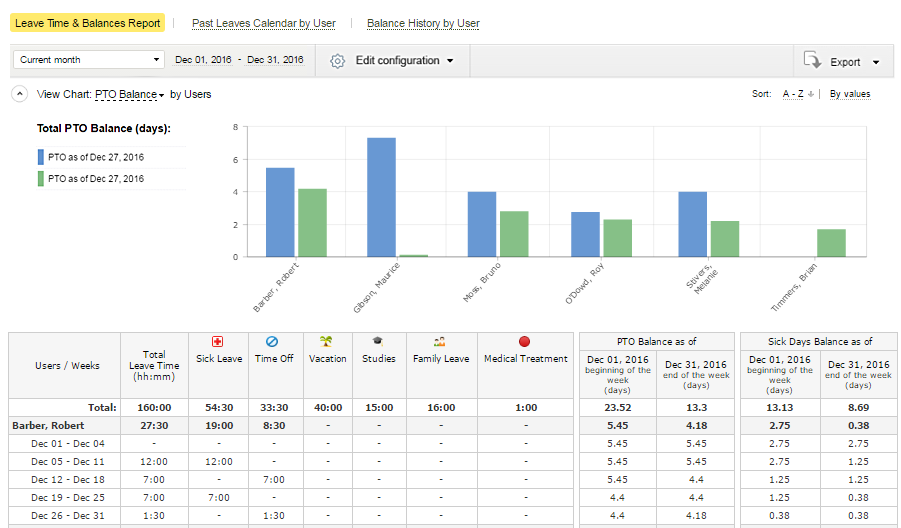
The software boasts unparalleled flexibility:
- You can create your own leave types and work types, set preferable time off accrual rules, and automate leave request approval if you like.
- Your employees can schedule their shift preferences, instantly access personal time off data, and request leave days in just a few clicks.
This means they can more effectively manage their work schedule around their personal lives, which lets you create a happier, more fulfilled workforce.
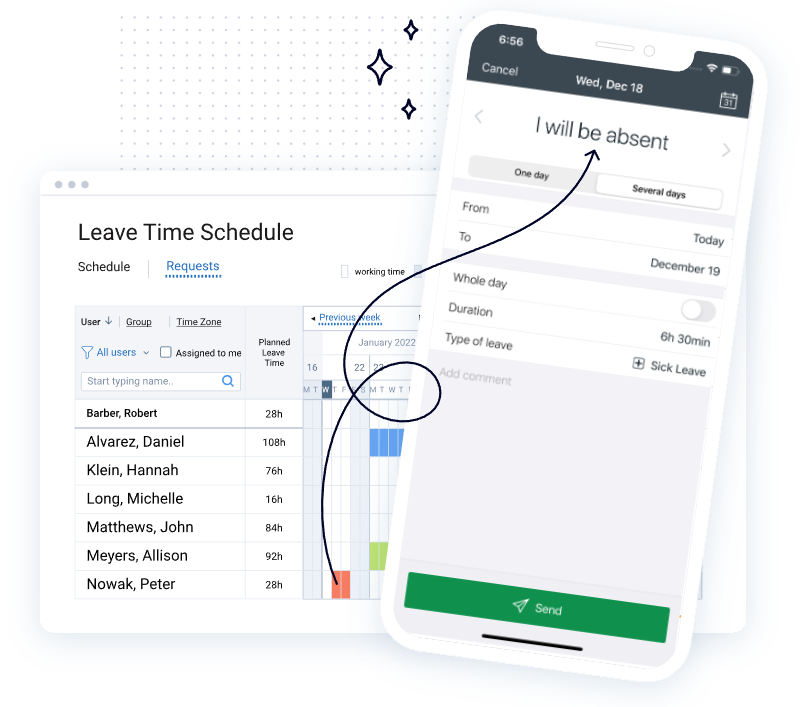
Pricing: Starting from $1.2 per user a month.
Best for: Teams of any size and from any industry.
2. Float
- Project planning
- Forecasting
- Scheduling
- Cost tracking
- Time tracking
Float is a cloud-based project management solution that helps businesses to efficiently manage their resources and schedules. It allows for the accurate tracking of employee utilization and project timelines, all in one easy-to-use interface.
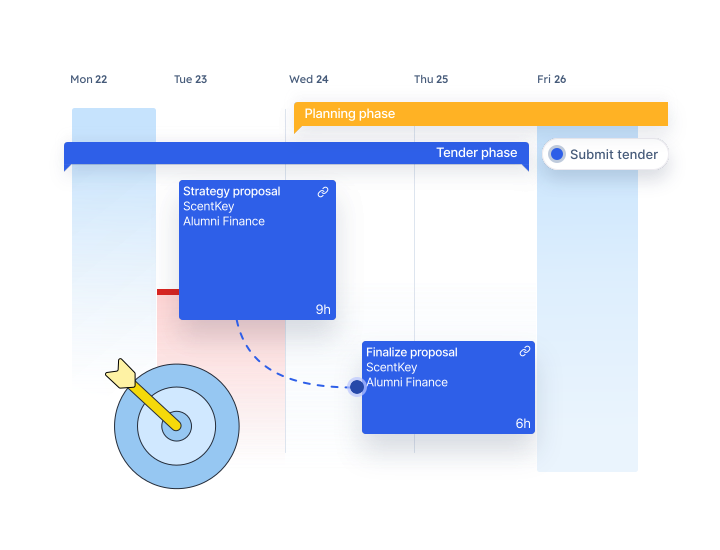
Float offers a plethora of capacity planning tools. It enables you to forecast your team’s availability and workload in the upcoming months. By having this bird’s eye view of your team’s capacity, you can identify potential bottlenecks and make informed decisions about hiring, rescheduling projects, or prioritizing tasks.
Float also allows you to allocate resources according to their availability, skills, and preferences, ensuring that the right people are working on the right projects at the right time. And the software’s simple drag-and-drop interface lets you quickly move tasks and projects around, adjust timelines, and visualize your team’s workload without a hitch.
Pricing: Starting from $6 per user a month.
Best for: Project-oriented teams.
3. Saviom
- Resource management
- Business intelligence
- Forecasting
- Scheduling
Saviom is an all-in-one solution that streamlines your entire workforce management process, providing you with real-time insights and making business-critical decisions a breeze.
Saviom allows you to take into account each team member’s skills, availability, and workload when scheduling resources and then assign tasks and projects to the best-suited individuals. Not only does this greatly reduce the risk of burnout and turnover but also ensures that every team member is working at their optimal capacity – a win-win situation!
Besides, Saviom provides powerful reporting and analytics that help you identify potential bottlenecks and capacity constraints before they become major issues. This way, you can adjust your project plans and resource allocation in real time, ensuring that your projects stay on track and within budget.
Best for: Resourceful businesses and large enterprises.
Pricing: No info available.
4. Resource Guru
- Scheduling
- Project timelines
- Leave management
- Forecasting
ResourceGuru is a cloud-based resource scheduling software that provides businesses with a streamlined solution for managing their workforce.
ResourceGuru gives you complete control over your team’s scheduling, so you always know who’s available and when. With powerful project reports and visual resource scheduling features, you’ll never double-book a staff member again.
But that’s not all – ResourceGuru allows you to accurately forecast your team’s capacity over time, so you can plan ahead for future projects and adjust your staffing levels accordingly. This advanced capability makes ResourceGuru an indispensable tool for managers looking to maximize their operational efficiency.
Best for: Small and medium-sized businesses.
Pricing: Starting from $4.16 per user a month.
5. Parallax
- Resource planning
- Forecasting
- Project financials
- Operations Intelligence
By leveraging the power of data analytics and visualizations, Parallax enables organizations to gain a deeper understanding of how their systems and processes are performing and identify areas where improvements can be made.
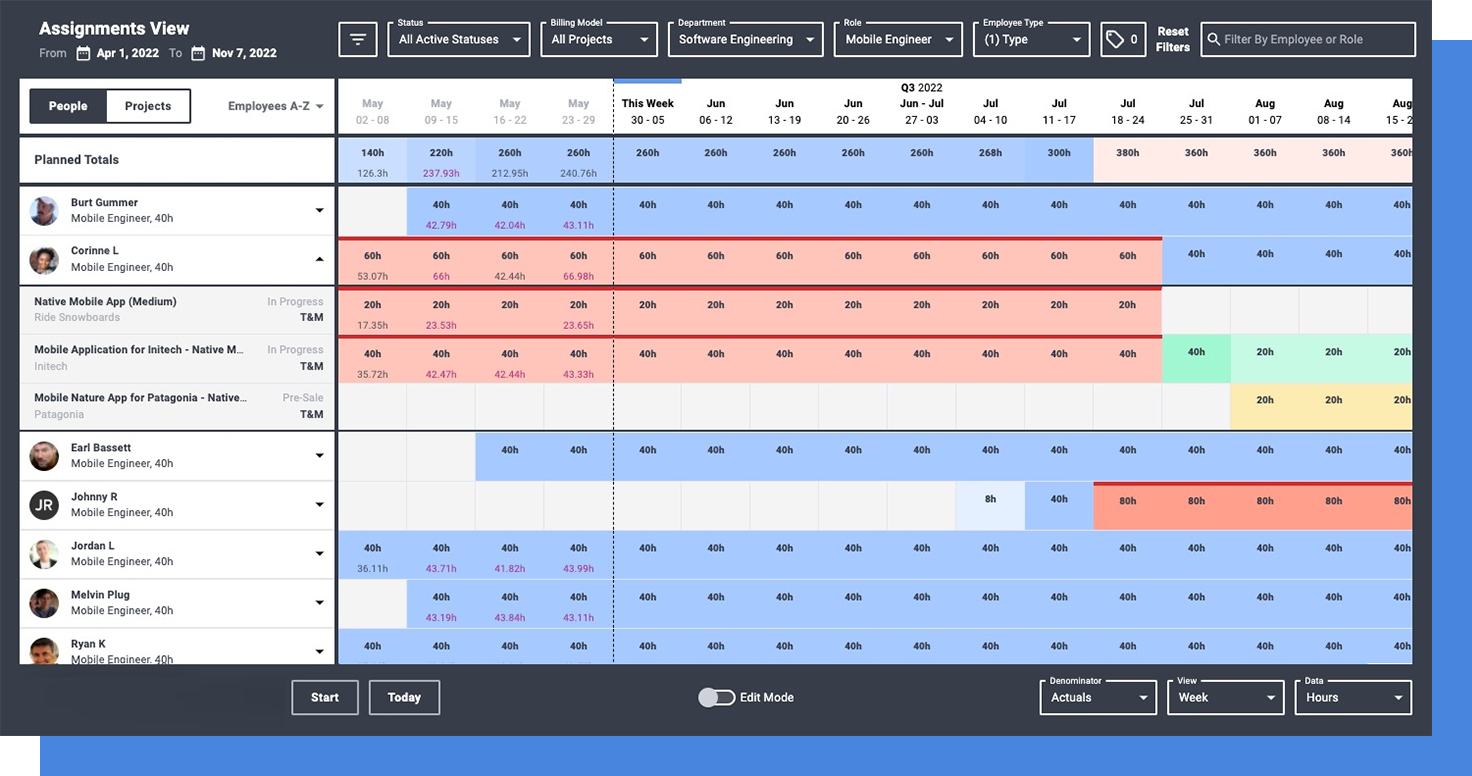
One of the key benefits of this capacity planning tool is that it allows organizations to forecast future demand based on historical trends and patterns. This is particularly useful for organizations that experience seasonality or other cyclical fluctuations in demand, as it enables them to proactively plan for peak periods and avoid capacity constraints.
Another way that Parallax facilitates capacity planning is by allowing organizations to perform scenario analysis. By simulating different scenarios and testing their impact on capacity utilization, you can identify potential challenges and proactively plan for them. This can help to mitigate risk, avoid disruption to operations, and ultimately improve customer satisfaction.
Best for: Large project-oriented businesses and sales teams.
Pricing: No info available.
Best Practices for Top-Notch Capacity Management
1. Track time and costs regularly
When you track the time and costs associated with projects, you’re essentially collecting valuable data on how long tasks take and how much they cost. This info is like gold when it comes to planning future projects. It gives you a clear picture of your team’s capabilities and resources, making it easier to estimate how much work they can handle without overcommitting.
Pro tip:
actiTIME really shines when it comes to time and cost tracking, which makes it a go-to tool for anyone looking to collect such data.
The software is pretty versatile, offering multiple time tracking modes that cater to different preferences and needs. We’ve got:
- The classic manual-entry timesheets for those who prefer to jot down hours at their own pace,
- A nifty mobile app equipped with one-click timers for tracking on the go,
- And even a fully automated browser extension for those who like things to happen without much fuss.
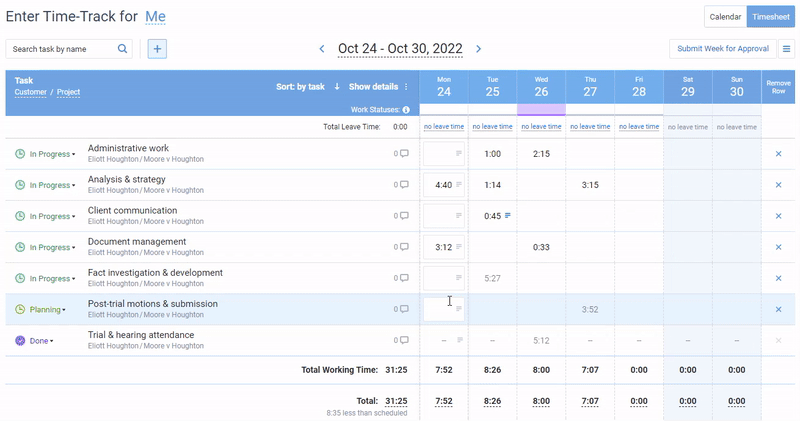
You can set custom pay rates for employees, and actiTIME will calculate staff-related expenses automatically, based on the hours you’ve tracked.
This feature is a game-changer for managing budgets effectively without getting buried in spreadsheets. Plus, you can churn out detailed performance reports to know who’s doing what, for how long, and how much it’s costing.
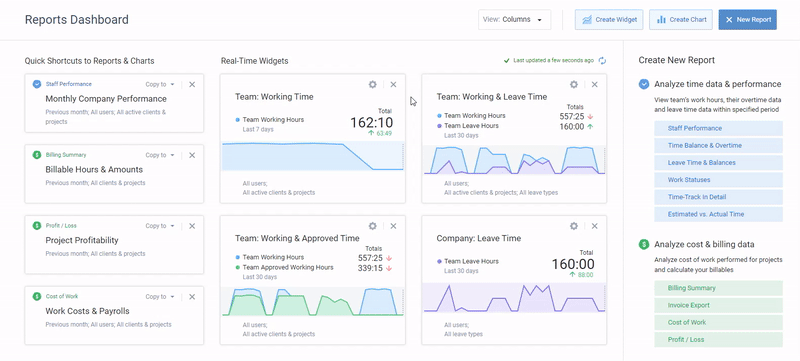
On top of that, actiTIME’s absence tracking features and actiPLANS integration help to improve capacity planning a great deal. This combo gives you a clear picture of workforce availability by tracking holiday times and planning for absences in advance – a must-have if you want to optimize your team’s time and business resources.
Explore actiTIME during a free 30-day trial 👈
2. Identify process bottlenecks
Have you ever tried to pour a gallon of water through a straw? No matter how much effort you put in, there’s a limit to how fast it can go.
Process bottlenecks are like traffic jams on a highway – they slow everything down and can throw a wrench into the smooth operations of your business.
When there’s a bottleneck, it means a particular stage is slowing down the flow of work, limiting the overall output your team can achieve.
Identifying these bottlenecks is crucial, and here’s a laid-back way to do it:
- Talk to your team: Sometimes the best insights come from the people on the front lines. Ask them where they feel held up or what frustrates them the most.
- Measure performance: Start gathering data on different parts of your process. Look for stages with longer completion times or lower output.
- Analyze workflows: Compare the performance at different stages. You can even map out each step of your workflow and then use that map to look for the spots where things pile up or slow down. Does stuff tend to get stuck at a particular decision point or phase in the workflow? Where do things seem to pile up? Which stage has the longest queue? Keep an eye out for repeating complaints or delays – they’re big, flashing signs pointing to your bottlenecks.
- Repeat regularly: Bottlenecks can shift as you make changes, so check your workflows regularly to keep your processes smooth.
3. Prioritize projects and tasks
Your resource and production capacities are always limited. Thus, you need to make sure that the most important stuff gets your attention, energy, and resources first.
Prioritizing is a way to achieve that.
It guarantees you’re not wasting precious resources on things that can either wait or don’t add significant value to your goals. Plus, it helps prevent the whole team from getting burned out from trying to juggle too much work at once.
It just makes everything smoother, you know?
Pro tip:
The critical path method offers a pretty straightforward way to prioritize tasks in projects.
Here’s how it works:
- Jot down every single thing you plan to complete in your project, no matter how big or small.
- Figure out the order. Some tasks depend on others to get started. Make a note of which tasks can’t begin until others are done.
- Calculate how long each task will take. Be realistic!
- Lay out your tasks in order, from start to finish, using your estimates. This is your project map.
- Look for the longest stretch of dependent tasks in your map. This is your critical path – the sequence of tasks that directly affects when your project will be done.
The key to using the critical path method effectively is to actually treat the tasks on that critical path as a priority, giving them the most attention and resources. If anything on the critical path gets delayed, your whole project gets delayed.
Other tasks? They’re important too, but if they’re off the path, they’ve got a bit more flexibility.
4. Test your systems
Checking how you work in different scenarios is like giving your car a test drive before a big road trip. It’s all about making sure you don’t end up stranded.
When you test your setup, systems, and processes, you can see whether they can handle the heavy lifting when the demand spikes or when you roll out new products and then find those weak spots before they cause real problems.
It’s a rehearsal of sorts, giving you a chance to understand how your internal systems perform under pressure, so you can tweak things and beef up resources where it’s needed.
After all, nobody wants their team or machinery to crash under pressure during a big sale or a product launch, right?
Conclusion
Capacity planning is not just for the logistics industry. It’s a great tool for all businesses – no matter their size or scope – to ensure they’re running at optimal levels and prepared for whatever the future may bring.
With the right capacity planning tools, strategies, and techniques in your corner, you can make sure your business never has too much or too little of anything. That way, you’ll be ready and able to tackle any challenge that comes your way with confidence and grace!